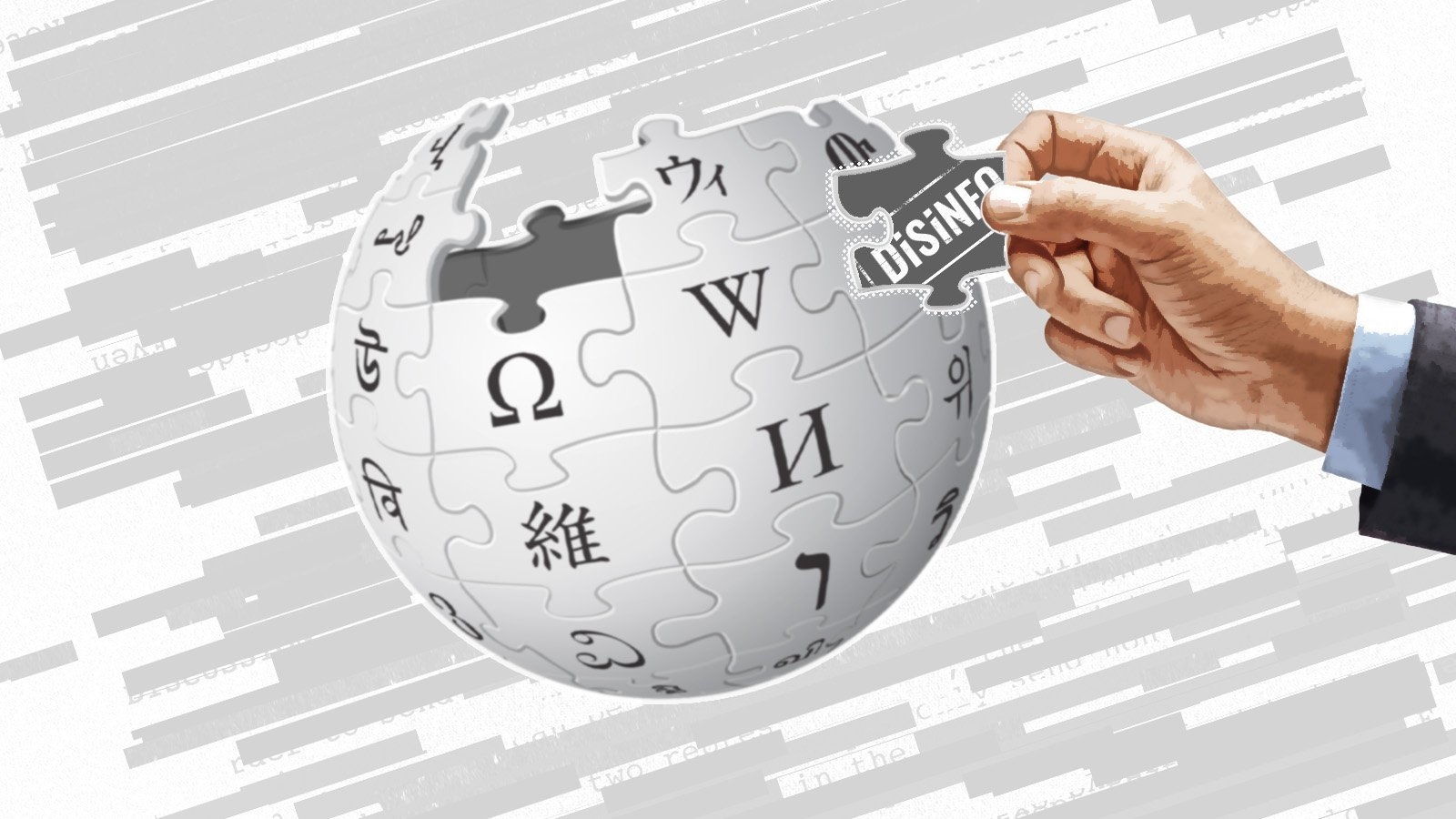
This article needs additional citations for verification.(November 2010) |
An elastic modulus (also known as modulus of elasticity (MOE)) is a quantity that describes an object's or substance's resistance to being deformed elastically (i.e., non-permanently) when a stress is applied to it.
Definition
The elastic modulus of an object is defined as the slope of its stress–strain curve in the elastic deformation region: A stiffer material will have a higher elastic modulus. An elastic modulus has the form:
where stress is the force causing the deformation divided by the area to which the force is applied and strain is the ratio of the change in some parameter caused by the deformation to the original value of the parameter.
Since strain is a dimensionless quantity, the units of will be the same as the units of stress.
Elastic constants and moduli
Elastic constants are specific parameters that quantify the stiffness of a material in response to applied stresses and are fundamental in defining the elastic properties of materials. These constants form the elements of the stiffness matrix in tensor notation, which relates stress to strain through linear equations in anisotropic materials. Commonly denoted as Cijkl, where i,j,k, and l are the coordinate directions, these constants are essential for understanding how materials deform under various loads.
Types of elastic modulus
Specifying how stress and strain are to be measured, including directions, allows for many types of elastic moduli to be defined. The four primary ones are:
- Young's modulus (E) describes tensile and compressive elasticity, or the tendency of an object to deform along an axis when opposing forces are applied along that axis; it is defined as the ratio of tensile stress to tensile strain. It is often referred to simply as the elastic modulus.
- The shear modulus or modulus of rigidity (G or
Lamé second parameter) describes an object's tendency to shear (the deformation of shape at constant volume) when acted upon by opposing forces; it is defined as shear stress over shear strain. The shear modulus is part of the derivation of viscosity.
- The bulk modulus (K) describes volumetric elasticity, or the tendency of an object to deform in all directions when uniformly loaded in all directions; it is defined as volumetric stress over volumetric strain, and is the inverse of compressibility. The bulk modulus is an extension of Young's modulus to three dimensions.
- Flexural modulus (Eflex) describes the object's tendency to flex when acted upon by a moment.
Two other elastic moduli are Lamé's first parameter, λ, and P-wave modulus, M, as used in table of modulus comparisons given below references. Homogeneous and isotropic (similar in all directions) materials (solids) have their (linear) elastic properties fully described by two elastic moduli, and one may choose any pair. Given a pair of elastic moduli, all other elastic moduli can be calculated according to formulas in the table below at the end of page.
Inviscid fluids are special in that they cannot support shear stress, meaning that the shear modulus is always zero. This also implies that Young's modulus for this group is always zero.
In some texts, the modulus of elasticity is referred to as the elastic constant, while the inverse quantity is referred to as elastic modulus.
Density functional theory calculation
Density functional theory (DFT) provides reliable methods for determining several forms of elastic moduli that characterise distinct features of a material's reaction to mechanical stresses.Utilize DFT software such as VASP, Quantum ESPRESSO, or ABINIT. Overall, conduct tests to ensure that results are independent of computational parameters such as the density of the k-point mesh, the plane-wave cutoff energy, and the size of the simulation cell.
- Young's modulus (E) - apply small, incremental changes in the lattice parameter along a specific axis and compute the corresponding stress response using DFT. Young’s modulus is then calculated as E=σ/ϵ, where σ is the stress and ϵ is the strain.
- Initial structure: Start with a relaxed structure of the material. All atoms should be in a state of minimum energy (i.e., minimum energy state with zero forces on atoms) before any deformations are applied.
- Incremental uniaxial strain: Apply small, incremental strains to the crystal lattice along a particular axis. This strain is usually uniaxial, meaning it stretches or compresses the lattice in one direction while keeping other dimensions constant or periodic.
- Calculate stresses: For each strained configuration, run a DFT calculation to compute the resulting stress tensor. This involves solving the Kohn-Sham equations to find the ground state electron density and energy under the strained conditions
- Stress-strain curve: Plot the calculated stress versus the applied strain to create a stress-strain curve. The slope of the initial, linear portion of this curve gives Young's modulus. Mathematically, Young's modulus E is calculated using the formula E=σ/ϵ, where σ is the stress and ϵ is the strain.
- Shear modulus (G)
- Initial structure: Start with a relaxed structure of the material. All atoms should be in a state of minimum energy with no residual forces. (i.e., minimum energy state with zero forces on atoms) before any deformations are applied.
- Shear strain application: Apply small increments of shear strain to the material. Shear strains are typically off-diagonal components in the strain tensor, affecting the shape but not the volume of the crystal cell.
- Stress calculation: For each configuration with applied shear strain, perform a DFT calculation to determine the resulting stress tensor.
- Shear stress vs. shear strain curve: Plot the calculated shear stress against the applied shear strain for each increment.The slope of the stress-strain curve in its linear region provides the shear modulus, G=τ/γ, where τ is the shear stress and γ is the applied shear strain.
- Bulk modulus (K)
- Initial structure: Start with a relaxed structure of the material. It’s crucial that the material is fully optimized, ensuring that any changes in volume are purely due to applied pressure.
- Volume changes: Incrementally change the volume of the crystal cell, either compressing or expanding it. This is typically done by uniformly scaling the lattice parameters.
- Calculate pressure: For each altered volume, perform a DFT calculation to determine the pressure required to maintain that volume. DFT allows for the calculation of stress tensors which provide a direct measure of the internal pressure.
- Pressure-volume curve: Plot the applied pressure against the resulting volume change. The bulk modulus can be calculated from the slope of this curve in the linear elastic region.The bulk modulus is defined as K=−VdV/dP, where V is the original volume, dP is the change in pressure, and dV is the change in volume.
See also
- Bending stiffness
- Dynamic modulus
- Elastic limit
- Elastic wave
- Flexural modulus
- Hooke's Law
- Impulse excitation technique
- Proportional limit
- Stiffness
- Tensile strength
- Transverse isotropy
- Elasticity tensor
References
- Askeland, Donald R.; Phulé, Pradeep P. (2006). The science and engineering of materials (5th ed.). Cengage Learning. p. 198. ISBN 978-0-534-55396-8.
- Beer, Ferdinand P.; Johnston, E. Russell; Dewolf, John; Mazurek, David (2009). Mechanics of Materials. McGraw Hill. p. 56. ISBN 978-0-07-015389-9.
- Schreiber, Edward; Anderson, O. L.; Soga, Naohiro (1974). Elastic constants and their measurement. New York: McGraw-Hill. ISBN 978-0-07-055603-4.
- Alasfar, Reema H.; Ahzi, Said; Barth, Nicolas; Kochkodan, Viktor; Khraisheh, Marwan; Koç, Muammer (2022-01-18). "A Review on the Modeling of the Elastic Modulus and Yield Stress of Polymers and Polymer Nanocomposites: Effect of Temperature, Loading Rate and Porosity". Polymers. 14 (3): 360. doi:10.3390/polym14030360. ISSN 2073-4360. PMC 8838186. PMID 35160350.
- Hadi, M. A.; Christopoulos, S.-R. G.; Chroneos, A.; Naqib, S. H.; Islam, A. K. M. A. (2022-08-18). "DFT insights into the electronic structure, mechanical behaviour, lattice dynamics and defect processes in the first Sc-based MAX phase Sc2SnC". Scientific Reports. 12 (1): 14037. doi:10.1038/s41598-022-18336-z. ISSN 2045-2322. PMC 9388654. PMID 35982080.
- Ahmed, Razu; Mahamudujjaman, Md; Afzal, Md Asif; Islam, Md Sajidul; Islam, R.S.; Naqib, S.H. (May 2023). "DFT based comparative analysis of the physical properties of some binary transition metal carbides XC (X = Nb, Ta, Ti)". Journal of Materials Research and Technology. 24: 4808–4832. doi:10.1016/j.jmrt.2023.04.147. ISSN 2238-7854.
- Choudhary, Kamal; Cheon, Gowoon; Reed, Evan; Tavazza, Francesca (2018-07-12). "Elastic properties of bulk and low-dimensional materials using van der Waals density functional". Physical Review B. 98 (1): 014107. arXiv:1804.01033. Bibcode:2018PhRvB..98a4107C. doi:10.1103/PhysRevB.98.014107. ISSN 2469-9950. PMC 7067065. PMID 32166206.
Further reading
- Hartsuijker, C.; Welleman, J. W. (2001). Engineering Mechanics. Volume 2. Springer. ISBN 978-1-4020-4123-5.
- De Jong, M.; Chen, Wei (2015). "Charting the complete elastic properties of inorganic crystalline compounds". Scientific Data. 2: 150009. Bibcode:2013NatSD...2E0009D. doi:10.1038/sdata.2015.9. PMC 4432655. PMID 25984348.
Conversion formulae | |||||||
---|---|---|---|---|---|---|---|
Homogeneous isotropic linear elastic materials have their elastic properties uniquely determined by any two moduli among these; thus, given any two, any other of the elastic moduli can be calculated according to these formulas, provided both for 3D materials (first part of the table) and for 2D materials (second part). | |||||||
3D formulae | Notes | ||||||
There are two valid solutions. | |||||||
Cannot be used when | |||||||
2D formulae | Notes | ||||||
Cannot be used when | |||||||
|
This article needs additional citations for verification Please help improve this article by adding citations to reliable sources Unsourced material may be challenged and removed Find sources Elastic modulus news newspapers books scholar JSTOR November 2010 Learn how and when to remove this message An elastic modulus also known as modulus of elasticity MOE is a quantity that describes an object s or substance s resistance to being deformed elastically i e non permanently when a stress is applied to it DefinitionThe elastic modulus of an object is defined as the slope of its stress strain curve in the elastic deformation region A stiffer material will have a higher elastic modulus An elastic modulus has the form d def stressstrain displaystyle delta stackrel text def frac text stress text strain where stress is the force causing the deformation divided by the area to which the force is applied and strain is the ratio of the change in some parameter caused by the deformation to the original value of the parameter Since strain is a dimensionless quantity the units of d displaystyle delta will be the same as the units of stress Elastic constants and moduliElastic constants are specific parameters that quantify the stiffness of a material in response to applied stresses and are fundamental in defining the elastic properties of materials These constants form the elements of the stiffness matrix in tensor notation which relates stress to strain through linear equations in anisotropic materials Commonly denoted as Cijkl where i j k and l are the coordinate directions these constants are essential for understanding how materials deform under various loads Types of elastic modulusSpecifying how stress and strain are to be measured including directions allows for many types of elastic moduli to be defined The four primary ones are Young s modulus E describes tensile and compressive elasticity or the tendency of an object to deform along an axis when opposing forces are applied along that axis it is defined as the ratio of tensile stress to tensile strain It is often referred to simply as the elastic modulus The shear modulus or modulus of rigidity G or m displaystyle mu Lame second parameter describes an object s tendency to shear the deformation of shape at constant volume when acted upon by opposing forces it is defined as shear stress over shear strain The shear modulus is part of the derivation of viscosity The bulk modulus K describes volumetric elasticity or the tendency of an object to deform in all directions when uniformly loaded in all directions it is defined as volumetric stress over volumetric strain and is the inverse of compressibility The bulk modulus is an extension of Young s modulus to three dimensions Flexural modulus Eflex describes the object s tendency to flex when acted upon by a moment Two other elastic moduli are Lame s first parameter l and P wave modulus M as used in table of modulus comparisons given below references Homogeneous and isotropic similar in all directions materials solids have their linear elastic properties fully described by two elastic moduli and one may choose any pair Given a pair of elastic moduli all other elastic moduli can be calculated according to formulas in the table below at the end of page Inviscid fluids are special in that they cannot support shear stress meaning that the shear modulus is always zero This also implies that Young s modulus for this group is always zero In some texts the modulus of elasticity is referred to as the elastic constant while the inverse quantity is referred to as elastic modulus Density functional theory calculationDensity functional theory DFT provides reliable methods for determining several forms of elastic moduli that characterise distinct features of a material s reaction to mechanical stresses Utilize DFT software such as VASP Quantum ESPRESSO or ABINIT Overall conduct tests to ensure that results are independent of computational parameters such as the density of the k point mesh the plane wave cutoff energy and the size of the simulation cell Young s modulus E apply small incremental changes in the lattice parameter along a specific axis and compute the corresponding stress response using DFT Young s modulus is then calculated as E s ϵ where s is the stress and ϵ is the strain Initial structure Start with a relaxed structure of the material All atoms should be in a state of minimum energy i e minimum energy state with zero forces on atoms before any deformations are applied Incremental uniaxial strain Apply small incremental strains to the crystal lattice along a particular axis This strain is usually uniaxial meaning it stretches or compresses the lattice in one direction while keeping other dimensions constant or periodic Calculate stresses For each strained configuration run a DFT calculation to compute the resulting stress tensor This involves solving the Kohn Sham equations to find the ground state electron density and energy under the strained conditions Stress strain curve Plot the calculated stress versus the applied strain to create a stress strain curve The slope of the initial linear portion of this curve gives Young s modulus Mathematically Young s modulus E is calculated using the formula E s ϵ where s is the stress and ϵ is the strain Shear modulus G Initial structure Start with a relaxed structure of the material All atoms should be in a state of minimum energy with no residual forces i e minimum energy state with zero forces on atoms before any deformations are applied Shear strain application Apply small increments of shear strain to the material Shear strains are typically off diagonal components in the strain tensor affecting the shape but not the volume of the crystal cell Stress calculation For each configuration with applied shear strain perform a DFT calculation to determine the resulting stress tensor Shear stress vs shear strain curve Plot the calculated shear stress against the applied shear strain for each increment The slope of the stress strain curve in its linear region provides the shear modulus G t g where t is the shear stress and g is the applied shear strain Bulk modulus K Initial structure Start with a relaxed structure of the material It s crucial that the material is fully optimized ensuring that any changes in volume are purely due to applied pressure Volume changes Incrementally change the volume of the crystal cell either compressing or expanding it This is typically done by uniformly scaling the lattice parameters Calculate pressure For each altered volume perform a DFT calculation to determine the pressure required to maintain that volume DFT allows for the calculation of stress tensors which provide a direct measure of the internal pressure Pressure volume curve Plot the applied pressure against the resulting volume change The bulk modulus can be calculated from the slope of this curve in the linear elastic region The bulk modulus is defined as K VdV dP where V is the original volume dP is the change in pressure and dV is the change in volume See alsoBending stiffness Dynamic modulus Elastic limit Elastic wave Flexural modulus Hooke s Law Impulse excitation technique Proportional limit Stiffness Tensile strength Transverse isotropy Elasticity tensorReferencesAskeland Donald R Phule Pradeep P 2006 The science and engineering of materials 5th ed Cengage Learning p 198 ISBN 978 0 534 55396 8 Beer Ferdinand P Johnston E Russell Dewolf John Mazurek David 2009 Mechanics of Materials McGraw Hill p 56 ISBN 978 0 07 015389 9 Schreiber Edward Anderson O L Soga Naohiro 1974 Elastic constants and their measurement New York McGraw Hill ISBN 978 0 07 055603 4 Alasfar Reema H Ahzi Said Barth Nicolas Kochkodan Viktor Khraisheh Marwan Koc Muammer 2022 01 18 A Review on the Modeling of the Elastic Modulus and Yield Stress of Polymers and Polymer Nanocomposites Effect of Temperature Loading Rate and Porosity Polymers 14 3 360 doi 10 3390 polym14030360 ISSN 2073 4360 PMC 8838186 PMID 35160350 Hadi M A Christopoulos S R G Chroneos A Naqib S H Islam A K M A 2022 08 18 DFT insights into the electronic structure mechanical behaviour lattice dynamics and defect processes in the first Sc based MAX phase Sc2SnC Scientific Reports 12 1 14037 doi 10 1038 s41598 022 18336 z ISSN 2045 2322 PMC 9388654 PMID 35982080 Ahmed Razu Mahamudujjaman Md Afzal Md Asif Islam Md Sajidul Islam R S Naqib S H May 2023 DFT based comparative analysis of the physical properties of some binary transition metal carbides XC X Nb Ta Ti Journal of Materials Research and Technology 24 4808 4832 doi 10 1016 j jmrt 2023 04 147 ISSN 2238 7854 Choudhary Kamal Cheon Gowoon Reed Evan Tavazza Francesca 2018 07 12 Elastic properties of bulk and low dimensional materials using van der Waals density functional Physical Review B 98 1 014107 arXiv 1804 01033 Bibcode 2018PhRvB 98a4107C doi 10 1103 PhysRevB 98 014107 ISSN 2469 9950 PMC 7067065 PMID 32166206 Further readingHartsuijker C Welleman J W 2001 Engineering Mechanics Volume 2 Springer ISBN 978 1 4020 4123 5 De Jong M Chen Wei 2015 Charting the complete elastic properties of inorganic crystalline compounds Scientific Data 2 150009 Bibcode 2013NatSD 2E0009D doi 10 1038 sdata 2015 9 PMC 4432655 PMID 25984348 Conversion formulaeHomogeneous isotropic linear elastic materials have their elastic properties uniquely determined by any two moduli among these thus given any two any other of the elastic moduli can be calculated according to these formulas provided both for 3D materials first part of the table and for 2D materials second part 3D formulae K displaystyle K E displaystyle E l displaystyle lambda G displaystyle G n displaystyle nu M displaystyle M Notes K E displaystyle K E 3K 3K E 9K E displaystyle tfrac 3K 3K E 9K E 3KE9K E displaystyle tfrac 3KE 9K E 3K E6K displaystyle tfrac 3K E 6K 3K 3K E 9K E displaystyle tfrac 3K 3K E 9K E K l displaystyle K lambda 9K K l 3K l displaystyle tfrac 9K K lambda 3K lambda 3 K l 2 displaystyle tfrac 3 K lambda 2 l3K l displaystyle tfrac lambda 3K lambda 3K 2l displaystyle 3K 2 lambda K G displaystyle K G 9KG3K G displaystyle tfrac 9KG 3K G K 2G3 displaystyle K tfrac 2G 3 3K 2G2 3K G displaystyle tfrac 3K 2G 2 3K G K 4G3 displaystyle K tfrac 4G 3 K n displaystyle K nu 3K 1 2n displaystyle 3K 1 2 nu 3Kn1 n displaystyle tfrac 3K nu 1 nu 3K 1 2n 2 1 n displaystyle tfrac 3K 1 2 nu 2 1 nu 3K 1 n 1 n displaystyle tfrac 3K 1 nu 1 nu K M displaystyle K M 9K M K 3K M displaystyle tfrac 9K M K 3K M 3K M2 displaystyle tfrac 3K M 2 3 M K 4 displaystyle tfrac 3 M K 4 3K M3K M displaystyle tfrac 3K M 3K M E l displaystyle E lambda E 3l R6 displaystyle tfrac E 3 lambda R 6 E 3l R4 displaystyle tfrac E 3 lambda R 4 2lE l R displaystyle tfrac 2 lambda E lambda R E l R2 displaystyle tfrac E lambda R 2 R E2 9l2 2El displaystyle R sqrt E 2 9 lambda 2 2E lambda E G displaystyle E G EG3 3G E displaystyle tfrac EG 3 3G E G E 2G 3G E displaystyle tfrac G E 2G 3G E E2G 1 displaystyle tfrac E 2G 1 G 4G E 3G E displaystyle tfrac G 4G E 3G E E n displaystyle E nu E3 1 2n displaystyle tfrac E 3 1 2 nu En 1 n 1 2n displaystyle tfrac E nu 1 nu 1 2 nu E2 1 n displaystyle tfrac E 2 1 nu E 1 n 1 n 1 2n displaystyle tfrac E 1 nu 1 nu 1 2 nu E M displaystyle E M 3M E S6 displaystyle tfrac 3M E S 6 M E S4 displaystyle tfrac M E S 4 3M E S8 displaystyle tfrac 3M E S 8 E M S4M displaystyle tfrac E M S 4M S E2 9M2 10EM displaystyle S pm sqrt E 2 9M 2 10EM There are two valid solutions The plus sign leads to n 0 displaystyle nu geq 0 The minus sign leads to n 0 displaystyle nu leq 0 l G displaystyle lambda G l 2G3 displaystyle lambda tfrac 2G 3 G 3l 2G l G displaystyle tfrac G 3 lambda 2G lambda G l2 l G displaystyle tfrac lambda 2 lambda G l 2G displaystyle lambda 2G l n displaystyle lambda nu l 1 n 3n displaystyle tfrac lambda 1 nu 3 nu l 1 n 1 2n n displaystyle tfrac lambda 1 nu 1 2 nu nu l 1 2n 2n displaystyle tfrac lambda 1 2 nu 2 nu l 1 n n displaystyle tfrac lambda 1 nu nu Cannot be used when n 0 l 0 displaystyle nu 0 Leftrightarrow lambda 0 l M displaystyle lambda M M 2l3 displaystyle tfrac M 2 lambda 3 M l M 2l M l displaystyle tfrac M lambda M 2 lambda M lambda M l2 displaystyle tfrac M lambda 2 lM l displaystyle tfrac lambda M lambda G n displaystyle G nu 2G 1 n 3 1 2n displaystyle tfrac 2G 1 nu 3 1 2 nu 2G 1 n displaystyle 2G 1 nu 2Gn1 2n displaystyle tfrac 2G nu 1 2 nu 2G 1 n 1 2n displaystyle tfrac 2G 1 nu 1 2 nu G M displaystyle G M M 4G3 displaystyle M tfrac 4G 3 G 3M 4G M G displaystyle tfrac G 3M 4G M G M 2G displaystyle M 2G M 2G2M 2G displaystyle tfrac M 2G 2M 2G n M displaystyle nu M M 1 n 3 1 n displaystyle tfrac M 1 nu 3 1 nu M 1 n 1 2n 1 n displaystyle tfrac M 1 nu 1 2 nu 1 nu Mn1 n displaystyle tfrac M nu 1 nu M 1 2n 2 1 n displaystyle tfrac M 1 2 nu 2 1 nu 2D formulae K2D displaystyle K mathrm 2D E2D displaystyle E mathrm 2D l2D displaystyle lambda mathrm 2D G2D displaystyle G mathrm 2D n2D displaystyle nu mathrm 2D M2D displaystyle M mathrm 2D Notes K2D E2D displaystyle K mathrm 2D E mathrm 2D 2K2D 2K2D E2D 4K2D E2D displaystyle tfrac 2K mathrm 2D 2K mathrm 2D E mathrm 2D 4K mathrm 2D E mathrm 2D K2DE2D4K2D E2D displaystyle tfrac K mathrm 2D E mathrm 2D 4K mathrm 2D E mathrm 2D 2K2D E2D2K2D displaystyle tfrac 2K mathrm 2D E mathrm 2D 2K mathrm 2D 4K2D24K2D E2D displaystyle tfrac 4K mathrm 2D 2 4K mathrm 2D E mathrm 2D K2D l2D displaystyle K mathrm 2D lambda mathrm 2D 4K2D K2D l2D 2K2D l2D displaystyle tfrac 4K mathrm 2D K mathrm 2D lambda mathrm 2D 2K mathrm 2D lambda mathrm 2D K2D l2D displaystyle K mathrm 2D lambda mathrm 2D l2D2K2D l2D displaystyle tfrac lambda mathrm 2D 2K mathrm 2D lambda mathrm 2D 2K2D l2D displaystyle 2K mathrm 2D lambda mathrm 2D K2D G2D displaystyle K mathrm 2D G mathrm 2D 4K2DG2DK2D G2D displaystyle tfrac 4K mathrm 2D G mathrm 2D K mathrm 2D G mathrm 2D K2D G2D displaystyle K mathrm 2D G mathrm 2D K2D G2DK2D G2D displaystyle tfrac K mathrm 2D G mathrm 2D K mathrm 2D G mathrm 2D K2D G2D displaystyle K mathrm 2D G mathrm 2D K2D n2D displaystyle K mathrm 2D nu mathrm 2D 2K2D 1 n2D displaystyle 2K mathrm 2D 1 nu mathrm 2D 2K2Dn2D1 n2D displaystyle tfrac 2K mathrm 2D nu mathrm 2D 1 nu mathrm 2D K2D 1 n2D 1 n2D displaystyle tfrac K mathrm 2D 1 nu mathrm 2D 1 nu mathrm 2D 2K2D1 n2D displaystyle tfrac 2K mathrm 2D 1 nu mathrm 2D E2D G2D displaystyle E mathrm 2D G mathrm 2D E2DG2D4G2D E2D displaystyle tfrac E mathrm 2D G mathrm 2D 4G mathrm 2D E mathrm 2D 2G2D E2D 2G2D 4G2D E2D displaystyle tfrac 2G mathrm 2D E mathrm 2D 2G mathrm 2D 4G mathrm 2D E mathrm 2D E2D2G2D 1 displaystyle tfrac E mathrm 2D 2G mathrm 2D 1 4G2D24G2D E2D displaystyle tfrac 4G mathrm 2D 2 4G mathrm 2D E mathrm 2D E2D n2D displaystyle E mathrm 2D nu mathrm 2D E2D2 1 n2D displaystyle tfrac E mathrm 2D 2 1 nu mathrm 2D E2Dn2D 1 n2D 1 n2D displaystyle tfrac E mathrm 2D nu mathrm 2D 1 nu mathrm 2D 1 nu mathrm 2D E2D2 1 n2D displaystyle tfrac E mathrm 2D 2 1 nu mathrm 2D E2D 1 n2D 1 n2D displaystyle tfrac E mathrm 2D 1 nu mathrm 2D 1 nu mathrm 2D l2D G2D displaystyle lambda mathrm 2D G mathrm 2D l2D G2D displaystyle lambda mathrm 2D G mathrm 2D 4G2D l2D G2D l2D 2G2D displaystyle tfrac 4G mathrm 2D lambda mathrm 2D G mathrm 2D lambda mathrm 2D 2G mathrm 2D l2Dl2D 2G2D displaystyle tfrac lambda mathrm 2D lambda mathrm 2D 2G mathrm 2D l2D 2G2D displaystyle lambda mathrm 2D 2G mathrm 2D l2D n2D displaystyle lambda mathrm 2D nu mathrm 2D l2D 1 n2D 2n2D displaystyle tfrac lambda mathrm 2D 1 nu mathrm 2D 2 nu mathrm 2D l2D 1 n2D 1 n2D n2D displaystyle tfrac lambda mathrm 2D 1 nu mathrm 2D 1 nu mathrm 2D nu mathrm 2D l2D 1 n2D 2n2D displaystyle tfrac lambda mathrm 2D 1 nu mathrm 2D 2 nu mathrm 2D l2Dn2D displaystyle tfrac lambda mathrm 2D nu mathrm 2D Cannot be used when n2D 0 l2D 0 displaystyle nu mathrm 2D 0 Leftrightarrow lambda mathrm 2D 0 G2D n2D displaystyle G mathrm 2D nu mathrm 2D G2D 1 n2D 1 n2D displaystyle tfrac G mathrm 2D 1 nu mathrm 2D 1 nu mathrm 2D 2G2D 1 n2D displaystyle 2G mathrm 2D 1 nu mathrm 2D 2G2Dn2D1 n2D displaystyle tfrac 2G mathrm 2D nu mathrm 2D 1 nu mathrm 2D 2G2D1 n2D displaystyle tfrac 2G mathrm 2D 1 nu mathrm 2D G2D M2D displaystyle G mathrm 2D M mathrm 2D M2D G2D displaystyle M mathrm 2D G mathrm 2D 4G2D M2D G2D M2D displaystyle tfrac 4G mathrm 2D M mathrm 2D G mathrm 2D M mathrm 2D M2D 2G2D displaystyle M mathrm 2D 2G mathrm 2D M2D 2G2DM2D displaystyle tfrac M mathrm 2D 2G mathrm 2D M mathrm 2D